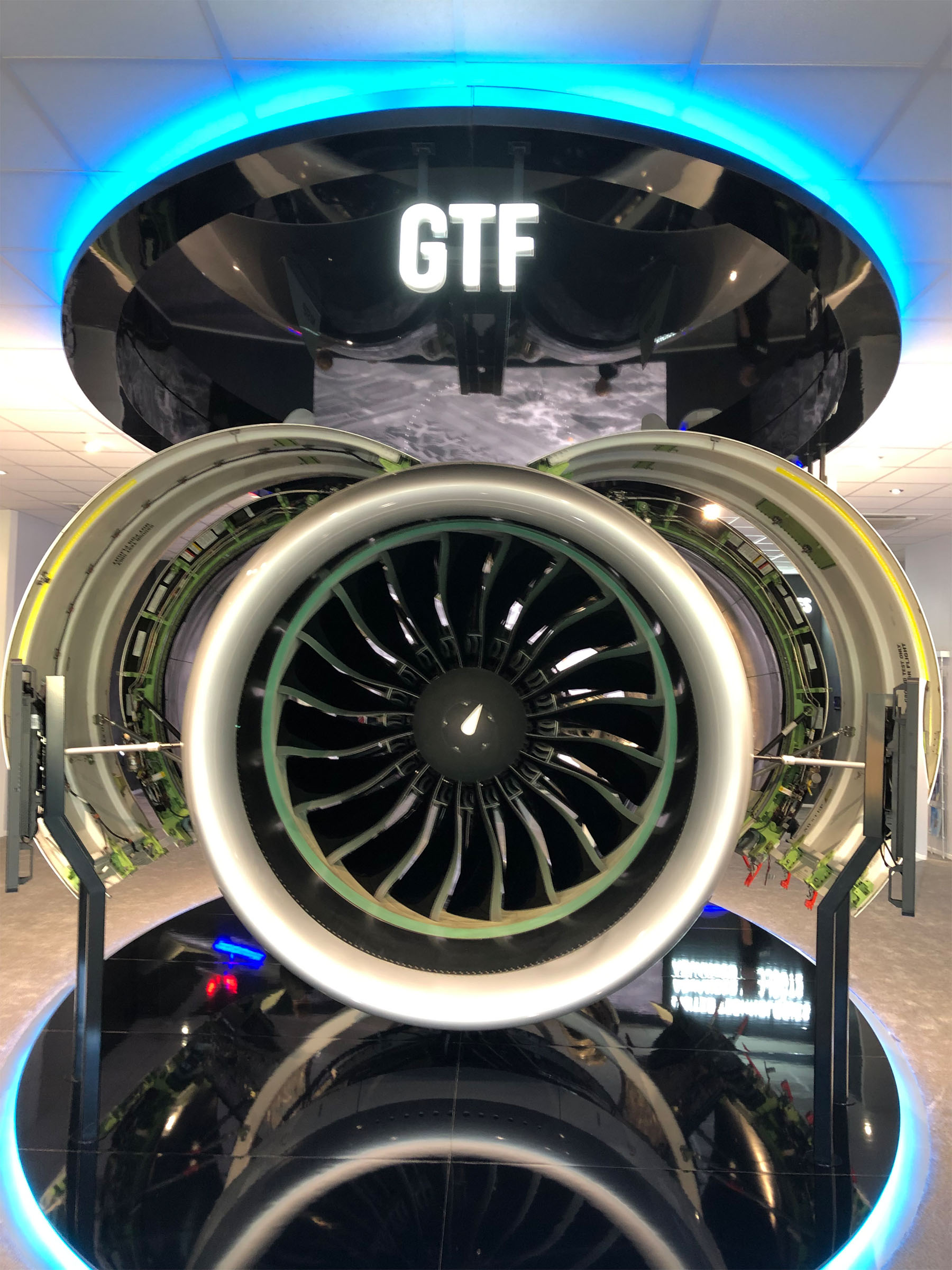
Pratt & Whitney estimates its GTF engine have saved customers more than 150 million gallons of fuel valued at $270 million USD, while avoiding 1.5 million tonnes of carbon emissions since the engine entered service in 2016.
Pratt & Whitney continues to introduce world-leading intuitive Industry 4.0 technologies – and drive innovation by developing new techniques and processes from Singapore for the global market – across manufacturing and aftermarket operations as part of its Intelligent Factory strategy. Pratt & Whitney is a division of United Technologies Corp. (UTX).
Pratt & Whitney’s Intelligent Factory strategy steps up from the Connected Factory pilot program launched last year. The use of advanced artificial intelligence (AI), robotic, automation and additive manufacturing technologies – underpinned by site-level and business-wide data analytics – will further enhance the level of operational effectiveness and insights across Pratt & Whitney’s Asia Pacific facilities in the next phase of its digital transformation.
Game-changing innovations developed from Singapore
Its blade and vane repair specialist, Turbine Overhaul Services, developed the first fully automated ultrasonic measurement system in Pratt and Whitney’s global operations from Singapore. It introduced an advanced robotic inspection of airfoil wall thickness to produce fast and reliable inspections, helping to free up inspector hours to perform more critical visual inspection tasks.
The industry’s first powder titanium turbine blades with titanium powder cladding using automated fiber optic has also been introduced by Turbine Overhaul Services. While laser cladding is a known technology in the aerospace sector, this newly developed process for the industry can adjust to incoming repair blades variation to enable predictable and dimensionally consistent build up that helps downstream process automation. This allows zero welding rework during repair, replacing the hot process of welding with a cool laser cladding process.
Pratt & Whitney is also making strong progress in additive manufacturing with the first-in-MRO application of 3D printing for aero-engine component detail at its Component Aerospace Singapore facility. This applies to the engine component of the PW4000 engine type that powers, for example, some models of the Airbus A330 and Boeing 777. Component Aerospace Singapore provides engine part repair for combustion chambers, fuel nozzle injectors and guides, tubes, ducts and manifolds.
Pioneering advanced AI and robotic applications for the MRO sector
Pratt & Whitney introduced pioneering robotic technologies in the MRO sector targeted at improving productivity in various processes. By growing key technologies like AI and automation, it creates flexibility and scalability in the applications, and this opens up a new level of speed and efficiency in delivering to the needs of customers.
Component Aerospace Singapore also introduced an automated fixture system using 12-armed robots to replace manual fixtures for tube repair, which is another first in the industry.
Pratt & Whitney Component Solutions, part repair specialist for compressor stators and seals, variable vanes and shrouds, is adopting a fully automated robotic loading process that incorporates a Computer Numerical Control (CNC) machine together with a Collaborative Robot (COBOT), enabling 24/7 operations without human supervision.
Turbine Overhaul Services has also integrated an AI-based proprietary Piece Part Inspection (PPI) technology that reduced turnaround time for crucial visual inspections of its PW2000, PW4000 and V2500 engines designed to improve quality and repeatability.
An end-to-end digital thread across the business
Pratt & Whitney’s digital-driven approach builds on its pioneering use of the Robotic Process Automation (RPA) to weave a digital thread across its operations from end to end. This will be boosted by a major Enterprise Resource Planning (ERP) update this year to unlock the full potential of data access, which will enable analytics for both site-level and business-wide insights.